锂离子电池的优缺点 - 锂离子电池制造
阳极与阴极的重量比
在电池运行期间不形成锂金属是非常重要的。 金属的沉积形成使电池内部短路的枝晶。 充电时的电压控制和电芯平衡有助于在很大程度上减少这个问题。 控制锂沉积的主要方法是电池中各个板的阳极与阴极容量之比。 阳极电极的可用容量比阴极高约 10% 。 这可以防止充电期间锂金属沉积在阳极上,因为阴极决定了电池的容量。 如果锂金属沉积在电极表面,它会与电解液发生反应并可能引发热失控。

图 21。 锂离子电池正负极容量比
(图片来源: Ralph J. Brodd 和 Kazuo Tagawa,锂离子电池进展,Walter A. van Schalkwijk 和 Bruno Scrosati(编辑),Kluwer Academic Publishers,纽约,第 272 页,2002 年。)
锂离子电池组装工艺锂离子电池的电池组装过程需要在涂有活性材料的正极和负极材料时精确和准确。 涂层工艺是确保高容量、高可靠性产品的关键因素。 如果涂层质量差,只能生产低性能电池。 准备活性物质的初始步骤决定了结果。
科恩和古托夫 [E. Cohen 和 E. Gutoff,现代涂层和干燥技术,Wiley-VCH,
New York, 1992]描述了一种方法,可以根据涂层浆料的流变性、所需的涂层精度和速度,为特定应用找到最佳涂层技术。
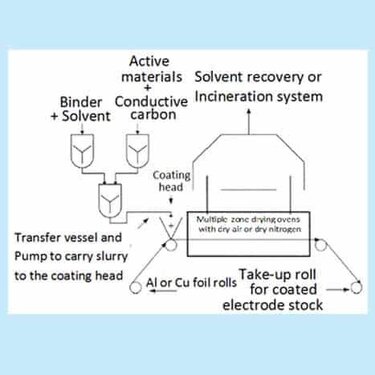
图 22。 阳极和阴极涂层工艺
(信用: Ralph J. Brodd 和 Kazuo Tagawain 在锂离子电池进展中,Walter A. van Schalkwijk 和 Bruno Scrosati(编辑),Kluwer Academic Publishers,纽约,第 273 页,2002 年。)
锂离子电池制造流程图
图 23。 锂离子电池制造流程图
[Ralph J. Brodd 和 Kazuo Tagawa 在锂离子电池方面的进展, Walter A. van Schalkwijk 和 Bruno Scrosati(编辑),Kluwer Academic Publishers,纽约,第 271 页,2002 年。]

图片来源:Electropaedia https://www.mpoweruk.com/battery_manufacturing.htm
图 24。 用原材料制造电极的流程图
锂离子电池组
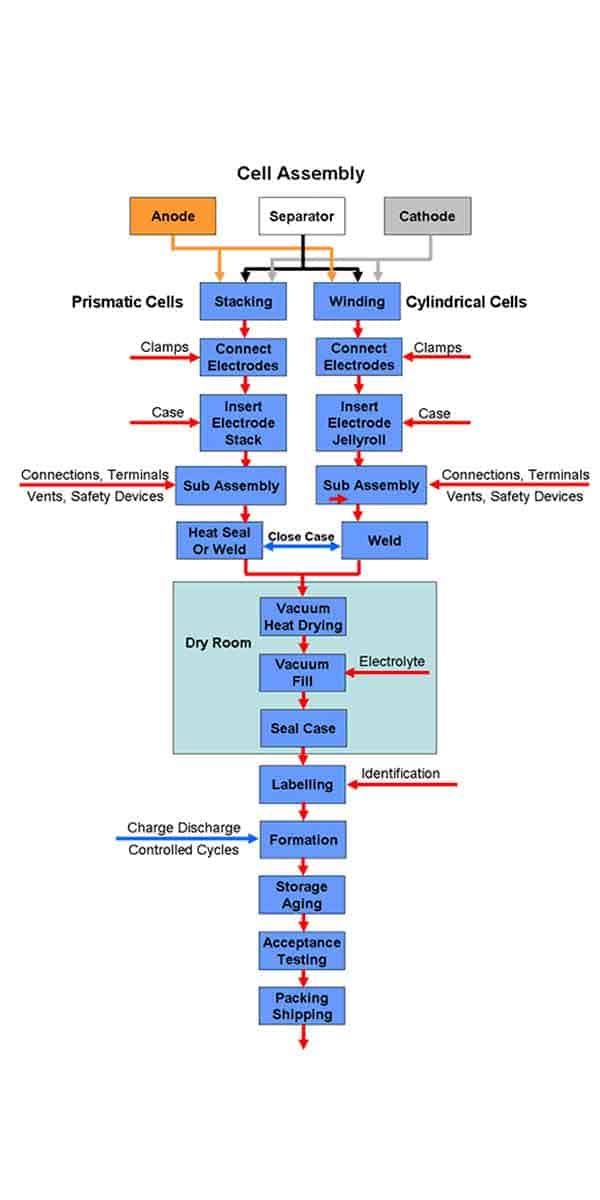



锂离子电池制造商在组装电芯时针对以下几点:
锂离子电池的设计必须在整个电极区域产生均匀的电流密度。 确保活性材料 (AM) 和集电器之间的良好接触 大表面积电极用于赋予电池高倍率性能。 这减少了极化,即由于电极反应动力学引起的电压损失,并降低了隔板两端的电压降。孔结构和导电碳的组合使活性材料具有良好的颗粒间接触。
活性材料、导电碳和集电器之间的良好接触对于活性材料的充分利用和高倍率性能期间的良好效率至关重要。
钴阴极混合物由 LiCoO2(一种黑色粉末)+ PVdF 粘合剂(一种白色半结晶含氟聚合物热塑性塑料)+ N-甲基吡咯烷酮(NMP,一种无色有机液体)作为溶剂制成。 由于 LICoO2 不导电,因此加入导电稀释剂(通常是炭黑)以提高 LiCoO2 的导电性。
材料的比例和数量由单元设计和混合器的尺寸决定。 在加入涂料溶剂和粘合剂之前,使用强烈混合程序将非导电活性材料和碳干混。
将混合物干混,使活性材料颗粒均匀地覆盖一层导电碳薄膜,从而改善 AM 和集电器网格(铝箔,20 毫米厚)之间的电接触,从而确保充分利用所有 AM。 聚合物 NMP 溶解在单独容器中的涂层溶剂中。 干混混合 然后将溶剂溶液合并以形成浆液。
溶剂添加用于调整用于涂布操作的浆料(或油漆)的粘度。 聚偏二氟乙烯 (PVdF) 是首选的粘合剂,并且 溶剂是 N-甲基吡咯烷酮 (NMP)。 来自混合操作的浆液被放置在密封容器中,作为涂层操作的储存器和传输介质。 使用齿轮泵或类似的精密泵从存储容器中泵出精确量的涂料浆液,以避免流体中的任何空气进入涂料头。
阳极混合物以类似的方式用硬碳、PVdF 粘合剂和 NMP 制备。 这种混合物涂在用作网格的铜箔(10 毫米厚)上。
阳极和阴极的两侧都进行了约 100 毫米的涂层。 对于一定体积的电池,通过减少涂层厚度,可以增加总表面积。 与水性电解质相比,所使用的有机电解质具有较低的电导率,因此这种较高的表面积将有助于高功率放电电池。
电极厚度取决于所需的最大功率。 锂离子电池制造技术的一个独特之处在于它允许使用相同的电极制造技术进行广泛的功率/能量比设计 [布鲁斯利,纳兹里第 651 页]。 但是合适的电流收集和标签、单元格形状和设计很重要。
电池组件:带涂层的箔通过烘箱蒸发溶剂并在箔上留下精确数量的活性物质。 许多涂料溶剂被归类为危险品,不能释放到大气中。 作为一种节省成本的措施,通常回收溶剂以在该过程中重新使用。 为避免对环境造成任何污染,可以焚烧溶剂。
大多数锂离子电池是圆柱形的。 将果冻卷压平以获得用于棱柱形电池的元件。
棱柱形电池有利于更好地填充体积,但在循环或老化时容易膨胀。 圆柱形电池罐在元件中提供更好的机械强度、良好的尺寸稳定性和均匀的压力。
涂层操作会产生与卷材长度相匹配的间断涂层。 绕线机设计为自动运行,可与干燥的阴极、阳极和隔板(厚度为 25 毫米或更小,PP 或 PE 或混合材料)的大卷一起使用。
操作首先将接片焊接到箔的未涂层部分。 然后绕线机将带材切割成适当的长度,并将阳极-隔膜-阴极的组合以果冻卷的方式缠绕成紧密的线圈或线轴。 随着绕线芯直径的增加,绕线机会自动补偿以在线圈直径增加时保持恒定的张力,以实现对直径的紧密公差。 棱柱形电池的椭圆风是一个更复杂和更慢的过程。
缠绕后,在插入罐中之前,检查线圈是否有内部短路。 钢罐应清洁并镀镍,以提供稳定的表面并在电池组装前最大限度地减少罐腐蚀。 阳极引线焊接到罐底,阴极引线焊接到安全阀。 电解质被添加到半组装的电池中。 组装完成,压接顶盖。
及早排除潜在的电池故障是一种经济措施,可以防止对坏电池进行更多工作。 将线轴插入罐中,以便罐提供恒定压力以将元件的组件保持在一起,从而消除它们之间出现空隙的任何机会。 一些制造商可能会插入心轴以稳定线圈的中心。
除非所有操作都在干燥室或干燥箱中进行,否则必须在电解液填充过程之前通过加热和真空去除活性材料中吸收的水分。
电解液的精确真空填充是为了确保电解液渗透并完全填充隔板和电极结构中的可用孔隙。 精密泵计量电解液良好运行所需的计算量。 总是所有制造商都使用LiPF 6 (一种无机白色结晶化合物)作为电解质,环状(EC,碳酸亚乙酯)或链状碳酸酯(DMC,碳酸二甲酯,DEC,碳酸二乙酯,或 EMC,碳酸甲乙酯等)是这种电解质盐的溶剂。
基于碳酸亚乙酯 (EC) 与碳酸二甲酯 (DMC) 和/或碳酸二乙酯 (DEC) 的溶剂混合物的电解质通常与“4 V”阴极(钴酸盐、镍酸盐和锰酸盐)结合用于锂离子电池,因为溶剂的高氧化电位。
用电解液填充电池后,通过放置在电池罐和顶板之间的聚合物垫圈或垫圈的受控压缩来密封电池。 聚合物垫圈密封件上的压力受到控制,以使其保持在聚合物的弹性极限内。 如果超过弹性极限,聚合物冷流并破坏密封。
每个制造商使用稍微不同的机械结构来密封电池,但最终结果基本相同。 通常,在电池顶部附近形成肩部或壁架。 这用作密封件的基础,并将果冻卷固定到位,并防止在振动和冲击的影响下伸缩或改变缠绕线轴的位置。
任何位置偏移都会导致电流分布发生变化,并导致高性能电池的循环寿命或锂电镀不良。 电池顶板密封件包含一个通风孔、一个正温度系数元件 (PTC) 和一个电流中断 (CID) 安全装置。 CID 和 PTC 都是安全装置,旨在激活和防止电池内部产生危险的温度和压力。 在并入顶部组件之前,检查每批设备是否正常运行。
密封后,可以对细胞进行清洗、夹套和贴标签。 它们被赋予一个序列号以追溯制造日期并识别所有电池组件(电极材料、电解质、隔板等)。 容量和电压信息与电池编号一起存储,稍后用于匹配电池组组装。
电池可以用玻璃与金属密封进行激光焊接,以提供持久的气密密封。 对于较大的电池,即使在滥用条件下,也必须更加小心以确保安全操作。
虽然上述过程是针对便携式电子产品中使用的小型密封电池进行的,但用于储能、空间和电动汽车应用的大型工业电池的过程遵循相同的总体轮廓。
锂离子电池——形成和老化组装后,锂离子未掺杂到阳极碳中,因此电池不显示电压。 在初始充电期间,来自 PAM LiCoO 2的一部分锂离子未掺杂成为 Li 1-x CoO 2 ,而这些锂离子掺杂到碳阳极 (C y ) 中成为 Li x C y 。 当充电电压达到 4.1 到 4.2 V 时, x的值约为 0.5。 (即,50%)表明已使用了来自 LiCoO 2的 50% 的 Li。
另一个需要注意的方面是,一部分掺杂的锂离子不会返回并保留在阳极中。 其中, x-dx锂离子不会影响容量。 这大约是 10% 到 20% 的不可逆锂,这意味着初始充电的效率为 80% 到 90%。 从第二个循环开始,不可逆量不再增加,电池显示出制造商设计的 100% 容量。
在清洗和夹套之后,但在形成过程开始之前,记录所有电池的电压和阻抗,以挑选出任何有缺陷的电池。 然后对电池进行第一次充电
(初始充电或地层充电)。 由于至少两个原因,首次充电的条件很重要:
1) 在阳极上形成固体电解质中间相(SEI) 层,以防止其在电池正常运行期间与电解质发生自发反应,以及 2) 在活性材料和电解质之间建立良好的电接触。 第一次充电遵循制造商推荐的电池充电程序,但通常以较低的电流开始,然后在充电期间大约三分之一时增加到正常充电电流。 电池在形成后可在充电和放电的电压限制内继续循环一或两个以上循环。
在形成或循环之后,电池电压和容量被测量并存储以供以后在电池选择过程中使用。 老化期在两周到一个月之间不等,具体取决于制造商。 储存后再次测量电池的电压。 储存期开始和结束时的电压差异用于挑选具有“软”或“微”短路的电池。 内部短路的电池在储存后电压会降低,并与正常的电压和容量分布分开。 可能有必要在地层形成后抽空较大的单元以除去地层气体。